Coating systems: Preserving, finishing, drying
inTEC offers you coating systems for steel assemblies and profiles, pipe interiors and exteriors, and laboratory equipment for test panel coating. Industry-specific solutions have also been developed for spraying small parts.
- Spray systems for preservation or for the application of top coats are built into existing transport structures or production lines, or fitted as separate lines. The spraying and drying process is automated after the material has been fed. Loading and unloading can be set to manual, semi-automatic or fully automatic.
- Airless spray guns are used to apply the paint. The parts are coated on all sides in a continuous process. The distance between the spray guns and the part is regulated by geometry. The sprayers are automatically switched on and off to reduce paint consumption, depending on the contour.
- Air routing is designed to keep heat loss and ventilation output to a minimum.
- The design is developed according to the specifications, the shape of the parts, the ambient conditions and the project requirements.
- All assemblies are designed for quick, easy cleaning and are accessible from the outside. The walls of the spray unit have been coated with anti-adhesive foil, making them easy to clean. Overspray is collected on foils and is filtered out via the exhaust in the dry filter system.
- Maintenance work is reduced to basic fittings only.
Coating systems for steel profiles and structures
Preservation line (pre-fabrication)
Configuration and models:
» Air blower station to remove contaminants and water residue
» Painting unit with airless spray guns
» Paint supply, paint supply room
» Manual or automatic loading and unloading, or integration in existing transport systems
Technical data:
Brochures:
Gallery:
Overview of coating systems
Preservation line
Top plate coating
︽ Steel structure solutions for top coating of steel assemblies
Top coating (post-fabrication)
Configuration and models:
» Painting unit with airless spray guns
» Paint supply, paint supply room
» Manual or automatic loading and unloading, or integration in existing transport systems
» Connection with upstream blasting system for material pretreatment
Technical data:
Gallery:
Overview of coating systems
Topcoating of welded structural beams
Topcoating of Headplates
Top coating of welded beams
Coating systems for piping
︽ Solutions for outer coating of pipes
Outer coating of pipes
Outer coating systems for pipes are available for individual pipe systems or for pipe batches.
Configuration and models:
» Air blower station to remove contaminants and water residue
» Separator for overspray for reuse: Depends on the paint used
» Paint supply, paint supply room
» Manual or automatic loading and unloading, or integration in existing transport systems
Technical data:
Brochures:
Industry press:
Videos:
Controls demo
UV-Tube coating
︽ Solutions for inner coating of pipes
Inner coating of pipes
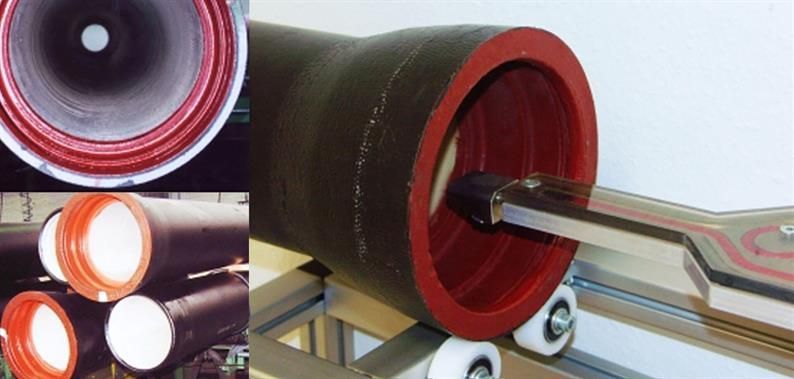
Inner coating systems for pipes are available for individual pipe systems or for pipe batches.
Configuration and models:
» Air blower station to remove contaminants and water residue
» Separator for overspray for reuse: Depends on the paint used
» Paint supply, paint supply room
» Manual or automatic loading and unloading, or integration in existing transport systems
Technical data:
Laboratory applications
︽ PB1 test sheet coating machine
PB1 test sheet coating machine
Our laboratory applications assist you with quality assurance and the development of new painting and coating procedures. The PB1 test sheet coating machine is used for the programmable and reproducible coating of test panels made of metal, plastic, wood, and glass.
The test sheet coating system is designed for installation in front of a filter/spray wall. The test sheet coating system is moveable on rollers at the place of installation. The place of installation must comply with EN 12215 and national health and safety regulations in the country of operation.
Test sheet coating machines are supplied with bespoke configurations and equipment variants. The test sheet coating system complies with the ATEX guideline (Ex II 3G T4).
Equipment variants:
Coating system
max. 2 spray guns with gravity feed cup
Number of spray types
7 (can be configured separately)
The number of spray types/programs supplied depends on the scope of the order.
Test panel holder
Magnetic strip for magnetic test panels
> Dimensions: 500 x 600 mm
> Max. thickness: 2,5 mm
Pot magnet for magnetic test panels with various dimensions
> Dimensions: 500 x 600 mm
> Max. thickness: 1,0 mm
With two suction cups for test panels made from wood, plastic, aluminum, and glass
> Dimensions: 50 x 150 mm
> Max. thickness: 1,5 mm
With six suction cups for test panels with lower surface roughness, free from grease and lubricating media
> Dimensions: 500 x 600 mm
> Max. thickness:
- 2,0 mm Sheet metal
- 1,5 mm Glass
- 4,0 mm Plastic
- 4,0 mm Wood
Technical data
Travel range of test sheet/spray gun
900 mm horizontal, maximum
600 mm vertical, maximum
Spray gun speed (horizontal)
0,3…0,8 m/s
Adjustable in 0.1 m/s increments
Test panel feed (vertical)
20…100 mm
Adjustable in 20 mm increments
Distance from spray gun to test panel
180…400 mm
Dimensions (height x width x depth)
1500 x 1250 x 760 mm
Weight
250 kg
ATEX class
Ex II 3G T4
Installation environment
spray booth in accordance with EN 12215,
max. VOC 100 mg/m3
Connection, electric
230 VAC 50 Hz, ExD
Ambient temperature
+ 10…30 °C
Brochures:
Industry press:
︽ PB2 test panel coating machines
PB2 test panel coating machines
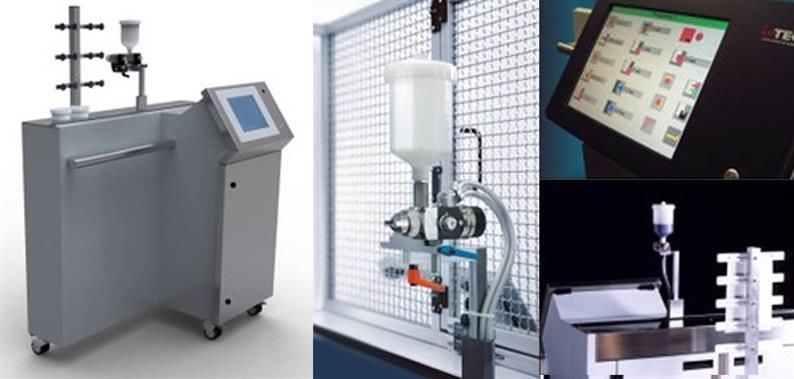
The test sheet coating system is designed for installation in front of a filter/spray wall. The test sheet coating system is moveable on rollers at the place of installation. The place of installation must comply with EN 12215 and national health and safety regulations in the country of operation.
Test sheet coating machines are supplied with bespoke configurations and equipment variants. The test sheet coating system complies with the ATEX guideline (Ex II 3G T4).
High-end
The PB2 test sheet coating system is operated via a touchscreen. The test data is organized in projects and can be distributed across several test sheet coating systems via a USB stick. It is therefore possible to exchange reproducible results independent of location.
Equipment variants:
Coating system
max. 2 spray guns with gravity feed cup
Optional: Paint supply pump
Project database
> Unlimited project storage with up to seven spray types/programs
> Store the projects on the hard disk or a USB stick
Anzahl Spritzarten/-programme
7 (individuell einstellbar)
Die Anzahl der gelieferten Spritzarten/-programme ist abhängig vom Bestellumfang.
Test panel holder
Magnetic strip for magnetic test panels
> Dimensions: 500 x 600 mm
> Max. thickness: 2,5 mm
Pot magnet for magnetic test panels with various dimensions
> Dimensions: 500 x 600 mm
> Max. thickness: 1,0 mm
With two suction cups for test panels made from wood, plastic, aluminum, and glass
> Dimensions: 50 x 150 mm
> Max. thickness: 1,5 mm
With six suction cups for test panels with lower surface roughness, free from grease and lubricating media
> Dimensions: 500 x 600 mm
> Max. thickness:
- 2,0 mm Sheet metal
- 1,5 mm Glass
- 4,0 mm Plastic
- 4,0 mm Wood
Technical data
Travel range of test sheet/spray gun
900 mm horizontal, maximum
600 mm vertical, maximum
Spray gun speed (horizontal)
0,3…0,8 m/s
Adjustable in 0.1 m/s increments
Test panel feed (vertical)
20…100 mm
Adjustable in 20 mm increments
Distance from spray gun to test panel
180…400 mm
Dimensions (height x width x depth)
1500 x 1250 x 760 mm
Weight
250 kg
Atex Class
Ex II 3G T4
Installation environment
Spray booth according to EN 12215,
max. VOC 100 mg/m3
Connection, electrical
230 VAC 50 Hz, ExD
Ambient temperature
+ 10…30 °C
Brochures:
Industry press:
︽ Test plate coating system PB3
Test plate coating system PB3
The test plate coating system is designed for installation in front of a filter/spray wall. The test plate coating system can be moved on rollers at the place of installation. The place of installation must fulfil the requirements of EN 16985, and the national health and safety regulations in the country of operation.
Test plate coating systems are supplied in bespoke configurations and equipment variants. The test plate coating system complies with the ATEX guideline (Ex II 3G T4).
High-end
The test plate coating system PB3 is operated via a touchscreen. The testing tasks are organized into projects, and can be distributed across several test plate coating systems via a USB stick. This makes it possible to exchange reproducible results independently of the location.
Equipment variants:
Coating gun
max. 2 coating guns
- with gravity cup
- Connection to material supply
When connected to material supply:
- Automatic volumetric measuring
- All air pressures measured and configurable digitally
- Rinsing of the system suction line
Material supply
- Material supply with gear pump
- Rinsing device with rinsing agent and compressed air
- Material container
- Rinsing agent container
- Residue tank
Project database
- Unlimited number or projects stored with individual spray types/programs and rinsing programs
- Stored on the hard drive or USB stick in CSV format
Number of spray
types/programs
6 (individually configurable)
The number of supplies spray types/programs depends on the scope of the order.
Rinsing programs
Storage of individual rinsing programs without step limit
Administrative programs
- File management
- Data backup
- Program manager
- System administration
Test plate holders
Magnetic strip for magnetic test plates:
- Dimensions: 600 x 320 mm
Test plates can be swivelled through 90° for “crosswise” spraying type
Optional: Vacuum holders for non-ferritic test plates.
Technical data:
Traversing range of test
plate/coating gun
- 1000 mm horizontal, maximum
- 600 mm vertical, maximum
Coating gun speed
(horizontal)
0.1…1.2 m/s
Adjustable in 0.001 m/s increments
Test plate feed
(vertical)
20…100 mm
Adjustable in 20 mm increments
Distance from test plate
to coating gun
200…400 mm
Dimensions (height x width x depth)
1620 x 1600 x 830 mm
Weight
450 kg
ATEX class
Ex II 3G T4
Installation environment
Spray booth as per EN 16985,
max. VOC 100 mg/m 3
Electric connection
230/400V AC, 50 Hz, 6A, ExD
Ambient temperature
+10…30 °C
Coating systems for industry-specific applications
︽ Coating systems for small parts and serial production
Coating systems for small parts
Metal, plastic or wooden series parts are coated using coating systems for small parts.
The material is pre-assembled on goods carriers. Goods can be loaded and unloaded from the goods carrier system manually, semi-automatically or automatically, e.g. using a robot.
The material is processed automatically in the coating system: e.g. cleaned with ionized air, painted, dried and cooled.
Cost-effective airless spray guns with atomized spray or electrostatic processes are used to apply the paint. The parts are coated on all sides in a continuous process. The distance between the spray guns and the part is regulated by geometry. The sprayers are automatically switched on and off to reduce paint consumption, depending on the contour
Overspray is filtered out with pre-filters and exhaust air filters.
Air routing is designed to keep heat loss and ventilation output to a minimum.
The walls of the spray unit have been coated with anti-adhesive foil, making them easy to clean.
Maintenance work is reduced to basic fittings only.
The design is developed according to the specifications, the shape of the parts, the ambient conditions and the project requirements.
︽ Coating systems for painting larger plastic components
Plastics
Spray systems for coating or larger plastic parts are built into existing transport structures or production lines, or fitted as separate lines.
The paint is applied using economical airless paint spray guns. The workpieces are coated on all sides in one pass. The distance between the paint spray guns and the workpiece is controlled depending on the geometry. The paint spray guns are switched on and off depending on the contour to reduce paint consumption.
Air routing is designed to keep heat loss and ventilation output to a minimum.
All assemblies are designed for quick, easy cleaning and are accessible from the outside.
The walls of the spray unit have been coated with anti-adhesive foil, making them easy to clean. Overspray is collected on foils and is filtered out via the exhaust in the dry filter system.
Maintenance work is reduced to basic fittings only.
The design is developed according to the specifications, the shape of the parts, the ambient conditions and the project requirements.
Industry press:
︽ Coating systems for coating mineral wool panels or mineral wool slats
Mineral wool
Spray systems for coating mineral wool panels or mineral wool slats are built into existing transport structures or production lines, or fitted as separate lines.
Airless spray guns are used to apply the paint. The parts are coated on all sides in a continuous process. The distance between the spray guns and the part is regulated by geometry. The sprayers are automatically switched on and off to reduce paint consumption, depending on the contour.
Air routing is designed to keep heat loss and ventilation output to a minimum.
All assemblies are designed for quick, easy cleaning and are accessible from the outside. The walls of the spray unit have been coated with anti-adhesive foil, making them easy to clean. Overspray is collected on foils and is filtered out via the exhaust in the dry filter system.
Maintenance work is reduced to basic fittings only.
The design is developed according to the specifications, the shape of the parts, the ambient conditions and the project requirements.